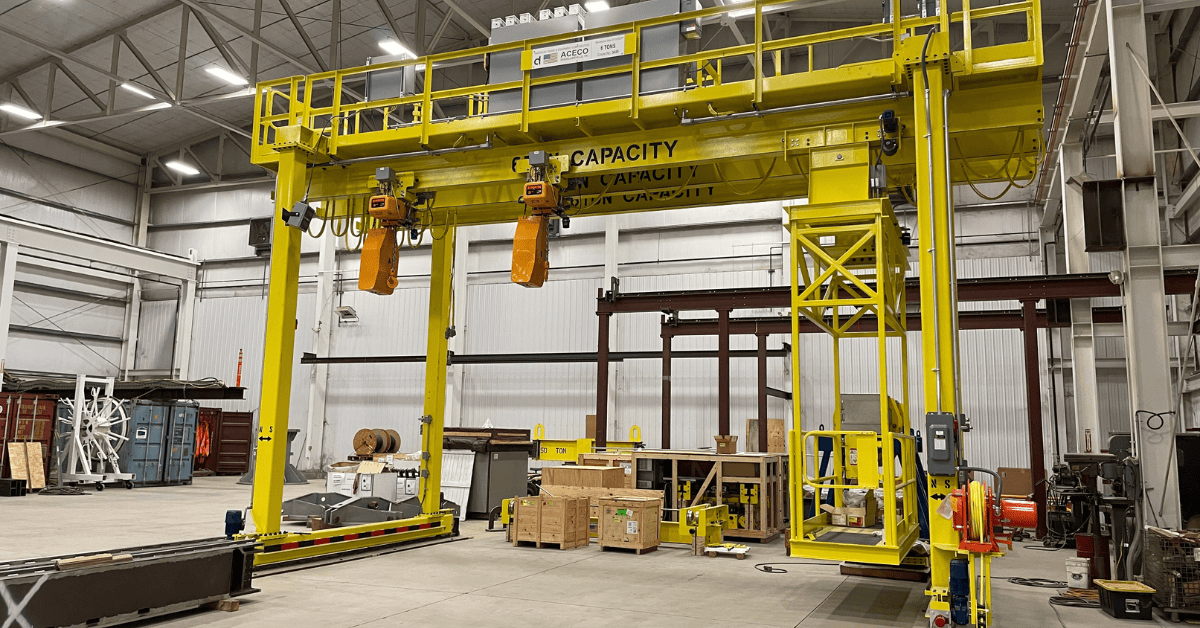
Z czego zbudowane są suwnice?
Poznaj budowę suwnic przemysłowych
W świecie przemysłowych systemów transportu bliskiego nie ma miejsca na przypadkowe rozwiązania. Suwnica, będąca jednym z najbardziej uniwersalnych i obciążanych mechanicznie urządzeń dźwignicowych, musi być zaprojektowana i zbudowana z największą precyzją. Konstrukcja suwnicy to nie tylko kwestia jej nośności – to złożony układ inżynieryjny, w którym każdy komponent odpowiada za konkretną funkcję i wpływa na bezpieczeństwo, trwałość oraz efektywność operacyjną całego zakładu.
Zanim zaczniemy mówić o mechanizmach, silnikach czy elektronice, musimy zrozumieć, że każdy element suwnicy – od dźwigarów po systemy sterowania – pracuje w ekstremalnych warunkach. Wysokie obciążenia, dynamiczne zmiany kierunku ruchu, drgania oraz wpływ środowiska (pył, temperatura, wilgotność) sprawiają, że błędy konstrukcyjne lub złe dopasowanie komponentów mogą prowadzić nie tylko do kosztownych awarii, ale też do zagrożenia życia i zdrowia pracowników.
To właśnie dlatego już na etapie projektowania konstrukcja suwnicy jest precyzyjnie dostosowywana do konkretnych warunków eksploatacyjnych. Dobór materiałów, parametry mechaniczne, zastosowane technologie spawania czy sposób rozmieszczenia napędów – wszystko to składa się na ogólną niezawodność i funkcjonalność urządzenia.
Wspólny rdzeń – mimo różnic, konstrukcja suwnicy ma stały schemat
Niezależnie od tego, czy mówimy o suwnicy pomostowej, bramowej czy kolumnowej, każda z nich składa się z zestawu podstawowych komponentów. Te elementy są zawsze obecne, choć różnią się skalą, geometrią i technologią wykonania. Dźwigary, czołownice, wózki jezdne, napędy, mechanizmy podnoszenia oraz układ sterowania – to konstrukcyjny szkielet, na którym opiera się funkcjonowanie urządzenia.
W praktyce oznacza to, że znajomość budowy suwnicy daje nam realną przewagę – zarówno przy jej zakupie, jak i późniejszym użytkowaniu czy modernizacji. Inżynierowie, technicy Utrzymania Ruchu, a także kadra odpowiedzialna za planowanie inwestycji powinni znać zależności między konstrukcją a funkcjonalnością, by podejmować decyzje świadomie i długoterminowo.
Dźwigary – kręgosłup konstrukcyjny każdej suwnicy
Dźwigary stanowią podstawowy element nośny w konstrukcji suwnicy. To one odpowiadają za przenoszenie większości obciążeń – zarówno własnej masy urządzenia, jak i dynamicznych sił działających podczas podnoszenia, opuszczania czy przemieszczania ładunków. Można je porównać do kręgosłupa całej konstrukcji – każda zmiana w ich geometrii lub wytrzymałości bezpośrednio wpływa na stabilność i bezpieczeństwo pracy urządzenia.
W suwnicach pomostowych najczęściej spotykamy dwa rozwiązania konstrukcyjne: dźwigar jednodźwigarowy i dwudźwigarowy. Wybór między nimi zależy od parametrów eksploatacyjnych, takich jak udźwig, rozpiętość oraz warunki montażowe. Dźwigary jednodźwigarowe pozwalają na niższy koszt inwestycyjny i łatwiejszy montaż, natomiast wersje dwudźwigarowe oferują znacznie większą nośność i możliwość montażu wózka między dźwigarami, co zmniejsza wysokość całkowitą układu.
Konstrukcja dźwigara to najczęściej stalowa belka skrzynkowa lub profilowa, wykonana ze stali konstrukcyjnej wysokiej jakości – najczęściej S355. Wymagana precyzja spawania i obróbki wymusza zastosowanie technologii spełniających normy PN-EN 1090 oraz kontroli zgodnych z wytycznymi F.E.M. (Federation Europeenne de la Manutention). Dodatkowo, dźwigary są zabezpieczane antykorozyjnie, zwłaszcza jeśli suwnica będzie pracować w środowiskach agresywnych lub na zewnątrz.
Bardzo ważnym aspektem projektowym jest sztywność konstrukcyjna – zarówno podłużna, jak i poprzeczna. Przemieszczenia i ugięcia dźwigarów muszą mieścić się w dopuszczalnych granicach określonych normami, aby zapobiec zmęczeniu materiału, deformacjom oraz przeciążeniom mechanizmów jezdnych. Prawidłowo zaprojektowany dźwigar to gwarancja stabilnej, precyzyjnej i bezpiecznej pracy suwnicy przez wiele lat.
Czołownice i zestawy kołowe – niezawodne prowadzenie suwnicy po torowisku
Czołownice są tym elementem konstrukcji suwnicy, który pełni funkcję łącznika między dźwigarem a układem jezdnym. To właśnie w nich montowane są zestawy kołowe, napędy jazdy oraz łożyskowania. W zależności od typu suwnicy i jej parametrów, czołownice mogą być konstrukcjami skrzynkowymi lub blachownicowymi, projektowanymi z myślą o zachowaniu maksymalnej sztywności i odporności na siły skręcające oraz uderzeniowe.
Koła suwnicowe, zamontowane w czołownicach, odpowiadają za płynne i precyzyjne przemieszczanie całej konstrukcji po torowisku. Wyróżniamy koła napędowe, które przekazują moment obrotowy z silnika, oraz bierne, które toczą się swobodnie. Ich wykonanie – najczęściej ze stali hartowanej lub żeliwa sferoidalnego – gwarantuje odporność na ścieranie oraz mikrouderzenia, jakie powstają podczas wjazdu na styk szyn lub w przypadku nierówności podtorza.
Bardzo istotnym aspektem jest sposób łożyskowania kół. Łożyska muszą być odpowiednio dobrane do warunków obciążeniowych i środowiskowych. W suwnicach pracujących w środowisku zapylonym lub przy dużej wilgotności, stosuje się uszczelnione rozwiązania łożyskowe, które minimalizują ryzyko przedostania się zanieczyszczeń.
Zestawy kołowe często wyposażane są w elementy regulacyjne, które pozwalają na precyzyjne ustawienie toru jazdy suwnicy. Odchylenia geometryczne mogą powodować nadmierne zużycie zarówno samych kół, jak i szyn, dlatego precyzyjne wykonanie czołownic i odpowiednia kalibracja w trakcie montażu są kluczowe dla długowieczności całego układu jezdnego.
Mechanizmy jazdy suwnicy – kontrola ruchu z milimetrową precyzją
Mechanizmy jazdy suwnicy odpowiadają za jej ruch wzdłuż torowiska i muszą być dostosowane do masy całkowitej konstrukcji oraz wymaganego tempa pracy. Ich zadaniem jest nie tylko napędzanie kół, ale również zapewnienie płynnego startu, hamowania oraz precyzyjnego pozycjonowania – zwłaszcza w przypadku pracy z ładunkami delikatnymi lub o dużych gabarytach.
Sercem mechanizmu jazdy jest silnik elektryczny – najczęściej asynchroniczny, trójfazowy, przystosowany do pracy z falownikiem. Umożliwia to płynną regulację prędkości oraz łagodne rozbiegi, co znacząco zmniejsza przeciążenia dynamiczne działające na konstrukcję. Silniki te dobierane są indywidualnie do wymagań projektowych i mogą być wyposażone w czujniki temperatury, enkodery, a także systemy hamulcowe.
Przekładnie stosowane w układach jazdy to najczęściej rozwiązania planetarne lub walcowe, oferujące wysoką sprawność i kompaktowe wymiary. W wielu przypadkach mamy do czynienia z tzw. motoreduktorami – zintegrowanymi zespołami silnika i przekładni, montowanymi bezpośrednio do ramy czołownicy.
Bardzo ważnym elementem jest zastosowanie falowników oraz układów sterowania, które umożliwiają synchronizację napędów, ograniczenie zużycia energii i precyzyjne sterowanie ruchem. W bardziej zaawansowanych aplikacjach stosuje się systemy jazdy synchronicznej, które eliminują ryzyko „szarpnięć” oraz nierównomiernego rozkładu sił w suwnicy o dużej rozpiętości.
Współczesne mechanizmy jazdy muszą sprostać nie tylko wymaganiom mechanicznym, ale również oczekiwaniom związanym z energooszczędnością, bezawaryjnością i łatwą diagnostyką. Dlatego coraz częściej integruje się je z systemami monitoringu online, pozwalającymi na bieżącą kontrolę parametrów pracy oraz przewidywanie zużycia komponentów.
Wózek suwnicy – newralgiczne centrum operacyjne całego układu
Wózek suwnicy to kluczowy moduł konstrukcyjny, który pełni funkcję mobilnej platformy dla układu podnoszenia. Jego precyzyjne działanie i niezawodność wpływają bezpośrednio na sprawność transportu bliskiego, a każda niedoskonałość w jego wykonaniu lub montażu odbija się na stabilności, bezpieczeństwie i komforcie pracy operatora. W praktyce to właśnie wózek odpowiada za przemieszczenie ładunku w osi poprzecznej względem toru jazdy suwnicy, umożliwiając manewrowanie z dużą precyzją nawet w ciasnych przestrzeniach produkcyjnych czy magazynowych.
Z technicznego punktu widzenia wózek składa się z ramy nośnej, układu jezdnego oraz napędu, ale jego sercem jest zespół podnoszenia – wciągnik lub wciągarka, zależnie od rodzaju suwnicy i przewidywanego udźwigu. Konstrukcja ramy musi być sztywna i odporna na skręcanie, a przy tym możliwie lekka, aby ograniczyć masę własną całego układu. Najczęściej wykonuje się ją ze stalowych profili spawanych lub giętych blach, zabezpieczonych antykorozyjnie metodą proszkową, galwaniczną lub natryskową.
Napęd wózka oparty jest na zestawach kołowych – podobnie jak w przypadku czołownic – z tym że tutaj kluczowe jest zapewnienie płynnego ruchu w ograniczonej przestrzeni dźwigara. W suwnicach dwudźwigarowych wózek porusza się po torach umieszczonych na górze dźwigarów, natomiast w konstrukcjach jednodźwigarowych najczęściej zawieszony jest pod dolnym pasem belki nośnej. To rozwiązanie wymusza inne podejście do prowadzenia i łożyskowania.
W nowoczesnych suwnicach stosuje się również systemy ograniczające rozbujanie ładunku, co ma szczególne znaczenie przy precyzyjnym pozycjonowaniu lub transporcie delikatnych elementów. Wózek może być wyposażony w czujniki odległości, enkodery pozycji, a także elementy diagnostyczne umożliwiające predykcyjną konserwację. Coraz częściej integruje się go także z systemami automatycznego sterowania lub synchronizacji pracy kilku urządzeń jednocześnie.
Układ podnoszenia – serce funkcjonalne suwnicy i wyznacznik jej potencjału
To właśnie układ podnoszenia odpowiada za podstawową funkcję każdej suwnicy – unoszenie i opuszczanie ładunku. W zależności od rodzaju urządzenia i wymagań aplikacyjnych, możemy mieć do czynienia z wciągnikami łańcuchowymi, linowymi lub wciągarkami bębnowymi, z których każda konfiguracja niesie ze sobą inne korzyści eksploatacyjne i ograniczenia. Wybór odpowiedniego rozwiązania jest jednym z kluczowych elementów procesu projektowego, wpływającym nie tylko na wydajność, ale też na bezpieczeństwo operacji transportowych.
Najczęściej stosowanym rozwiązaniem w suwnicach przemysłowych są wciągniki linowe, które charakteryzują się dużą żywotnością, możliwością pracy z większym udźwigiem oraz płynną kontrolą prędkości. Kluczowe komponenty tego układu to silnik podnoszenia, przekładnia redukcyjna, bęben linowy, prowadnica liny, hamulec elektromagnetyczny oraz zestaw czujników krańcowych. Każdy z tych elementów musi być optymalnie dobrany do specyficznych warunków pracy suwnicy – począwszy od częstotliwości cykli roboczych, po charakterystykę przemieszczanych ładunków.
Dobrej klasy układ podnoszenia musi zapewniać stabilne, kontrolowane i bezpieczne manewrowanie ładunkiem, niezależnie od jego masy i środka ciężkości. Zastosowanie falowników i systemów łagodnego rozruchu pozwala minimalizować drgania oraz ograniczać zużycie mechaniczne podzespołów. Niezwykle istotna jest również precyzyjna kontrola pozycji – zwłaszcza w aplikacjach zautomatyzowanych, gdzie każdy milimetr ma znaczenie.
W nowoczesnych suwnicach systemy podnoszenia są często wyposażone w redundancję bezpieczeństwa. Oprócz głównego hamulca stosuje się dodatkowe zabezpieczenia, które reagują w przypadku przeciążenia, zerwania liny czy awarii napędu. Standardem staje się również ciągły monitoring parametrów pracy – temperatury, wibracji, obciążenia – co znacząco zwiększa żywotność całego układu i pozwala planować serwis z wyprzedzeniem.
Zasilanie i sterowanie – krwiobieg i układ nerwowy współczesnych suwnic
Choć często pomijany w kontekście mechaniki, układ zasilania i sterowania suwnicy jest równie istotny jak elementy konstrukcyjne. To od jego jakości i konfiguracji zależy płynność ruchu, bezpieczeństwo pracy oraz możliwość wdrożenia automatyzacji i integracji z innymi systemami produkcyjnymi. Nowoczesne suwnice to w dużej mierze urządzenia elektro-mechaniczne, w których komponenty elektroniczne odpowiadają za synchronizację, diagnostykę i precyzyjne sterowanie każdym ruchem.
Zasilanie suwnic realizowane jest zazwyczaj za pomocą przewodów płaskich w systemach festonowych lub poprzez szynoprzewody z odbierakami prądu. Wybór zależy od charakterystyki pracy – systemy szynowe zapewniają większą niezawodność w trudnych warunkach, podczas gdy kable festonowe pozwalają na łatwiejszy montaż i serwis. Wózki suwnic oraz wciągniki mogą być zasilane osobnym obwodem, z zabezpieczeniami różnicowoprądowymi i wyłącznikami krańcowymi chroniącymi przed niekontrolowanym ruchem.
Sterowanie suwnicą to dziś znacznie więcej niż tylko proste przyciski w kasecie kablowej. Coraz częściej stosuje się systemy zdalnego sterowania radiowego, które pozwalają operatorowi pracować z bezpiecznej odległości, z zachowaniem pełnej kontroli nad procesem. W suwnicach pracujących w systemach produkcji ciągłej lub logistyki wysokiego składowania wdraża się sterowanie automatyczne oparte o sterowniki PLC, systemy SCADA lub dedykowane panele operatorskie HMI.
Nie bez znaczenia jest również integracja systemów suwnicowych z infrastrukturą zakładu. Możliwość połączenia z oprogramowaniem ERP lub MES pozwala na śledzenie cykli pracy, zużycia energii, lokalizacji ładunków czy efektywności operacyjnej. Taka cyfrowa integracja zmienia sposób postrzegania suwnicy – z urządzenia dźwignicowego staje się ona realnym ogniwem w łańcuchu wartości całego zakładu produkcyjnego.