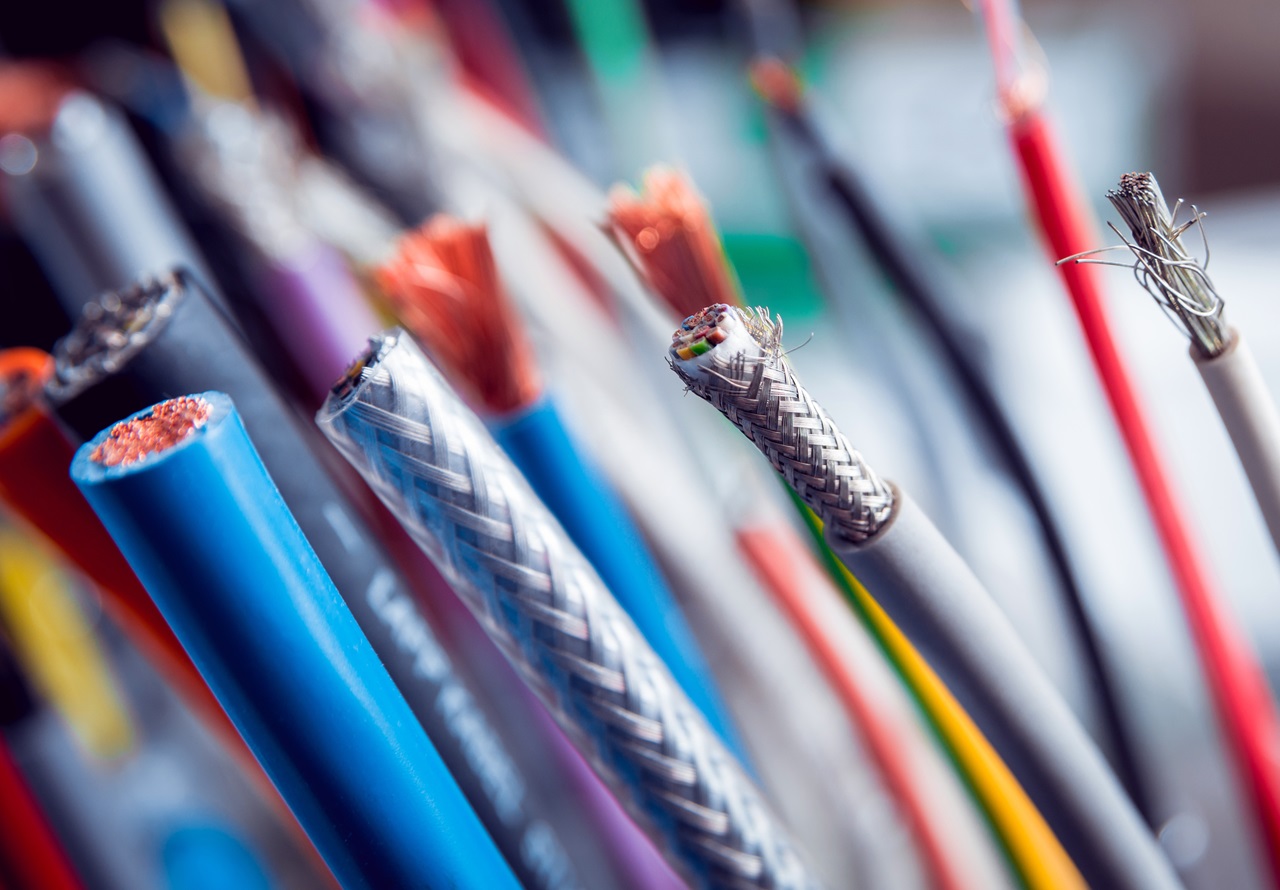
Przewody zasilające i sterownicze w urządzeniach dźwignicowych
Typowe środowiska pracy urządzeń dźwignicowych a wymagania wobec przewodów
W każdej aplikacji dźwignicowej — czy to w hali produkcyjnej, magazynie wysokiego składowania, czy w warunkach zewnętrznych — przewody zasilające i sterownicze muszą sprostać znacznie wyższym wymaganiom niż klasyczne okablowanie przemysłowe. To właśnie warunki środowiskowe, w których eksploatowane są suwnice, żurawie czy wciągniki, determinują dobór odpowiednich kabli i decydują o ich żywotności oraz niezawodności w długiej perspektywie. Nawet najlepiej zaprojektowany układ elektryczny nie zadziała poprawnie, jeśli zastosowane przewody nie będą dostosowane do realnych warunków pracy.
Zmienna temperatura, wilgotność i promieniowanie UV – wyzwania w aplikacjach zewnętrznych
Urządzenia dźwignicowe bardzo często pracują na zewnątrz – w strefach załadunku, portach przeładunkowych, magazynach otwartych czy zakładach przetwórstwa surowców. W takich przypadkach przewody muszą być odporne na promieniowanie UV, opady atmosferyczne, skrajne wahania temperatur oraz intensywne promienie słoneczne, które w ciągu kilku sezonów potrafią zniszczyć źle dobraną izolację.
Dobrej jakości przewód przeznaczony do pracy na zewnątrz powinien mieć powłokę odporną na działanie promieniowania ultrafioletowego oraz zabezpieczoną przed absorpcją wilgoci. Warto tu zwrócić uwagę na typ zastosowanego tworzywa – klasyczne PVC w takich warunkach traci elastyczność i może pękać, podczas gdy PUR czy TPE zachowują swoje właściwości mechaniczne nawet przy -30°C.
Kurz, pył, oleje i substancje chemiczne – codzienność zakładów przemysłowych
W halach produkcyjnych przewody narażone są nie tyle na warunki atmosferyczne, ile na silne zapylenie, działanie mgieł olejowych, chłodziw, smarów oraz cząstek ściernych pochodzących z obróbki metali czy tworzyw sztucznych. Praca w takim środowisku oznacza konieczność stosowania przewodów o zwiększonej odporności chemicznej i mechanicznej.
Nie mniej istotna jest odporność na ścieranie – przewody poruszające się w systemach festonowych czy prowadnikach kablowych są w ciągłym ruchu i narażone na tarcie o elementy metalowe. Izolacje nieprzystosowane do takich obciążeń bardzo szybko się wycierają, co prowadzi do mikropęknięć, uszkodzeń ekranu, a w konsekwencji – do zwarć, zakłóceń transmisji sygnału lub całkowitej awarii zasilania.
W przypadku pracy w pobliżu agresywnych chemikaliów – np. w przemyśle chemicznym, farmaceutycznym lub spożywczym – przewody muszą być zgodne z określonymi normami odporności na kontakt z olejami mineralnymi, rozpuszczalnikami, zasadami czy substancjami żrącymi. Zignorowanie tych aspektów może oznaczać konieczność przedwczesnej wymiany całej instalacji kablowej już po kilku miesiącach pracy.
Dynamiczne obciążenia mechaniczne – przewody w ciągłym ruchu
Jedną z cech charakterystycznych urządzeń dźwignicowych jest ich dynamiczny tryb pracy – wciągniki, wózki suwnicowe czy całe mosty są niemal nieustannie w ruchu. Oznacza to, że przewody są zginane, skręcane i rozciągane w każdym cyklu roboczym. Tylko specjalistyczne przewody do aplikacji ruchomych są w stanie sprostać takim warunkom bez utraty funkcji.
Kluczowe są tu takie parametry jak minimalny promień gięcia, liczba cykli zgięcia oraz odporność na mikropęknięcia izolacji. Przewody do prowadników czy firan kablowych muszą mieć odpowiednio zaprojektowaną konstrukcję wewnętrzną – żyły skręcone z odpowiednim skokiem, ekranowanie odporne na zmęczenie mechaniczne oraz izolację o wysokiej odporności na ścieranie i uderzenia.
Ignorowanie tych właściwości to prosta droga do awarii: zwarcia, niestabilność zasilania, przerwy w transmisji sygnałów z enkoderów, błędy w komunikacji z falownikami – wszystko to może wynikać z zastosowania nieodpowiedniego typu przewodu do aplikacji ruchomej.
Przewody zasilające – jak przenosić moc bez strat i ryzyka?
Zasilanie urządzeń dźwignicowych to zagadnienie, które wymaga nie tylko inżynierskiej precyzji, ale i głębokiego zrozumienia charakterystyki pracy suwnic, żurawi czy wciągarek. Źle dobrane przewody zasilające mogą prowadzić do przegrzewania się instalacji, niestabilnej pracy falowników, nieprawidłowego działania napędów, a w skrajnych przypadkach – do całkowitej awarii systemu. Niezawodne dostarczenie energii do każdego punktu układu dźwignicowego to fundament jego bezpieczeństwa i ciągłości pracy. A to zaczyna się właśnie od prawidłowego zaprojektowania i doboru przewodów.
Dobór przekroju – fundament stabilnego zasilania
Pierwszym i najważniejszym krokiem w doborze przewodów zasilających do suwnicy jest określenie ich przekroju. To parametr, który bezpośrednio wpływa na poziom strat napięcia, nagrzewanie się kabla i bezpieczeństwo całej instalacji. Przewód o zbyt małym przekroju będzie przeciążany prądowo, co doprowadzi do jego przegrzewania, uszkodzeń izolacji, a w dalszej perspektywie – do zakłóceń w działaniu systemu i zwiększenia ryzyka pożaru.
Przy projektowaniu instalacji należy uwzględnić długość trasy, moc urządzenia oraz typ pracy (ciągła, cykliczna, intensywna). Istotna jest także liczba uruchomień na godzinę oraz ewentualne przeciążenia rozruchowe. Przewód musi być dobrany tak, aby nawet w najbardziej obciążonym cyklu pracy jego temperatura nie przekraczała dopuszczalnych norm dla danej izolacji.
Warto również zwrócić uwagę na napięcie zasilające – przy zasilaniu urządzeń na 400 V i dużych długościach linii, niekontrolowany spadek napięcia może skutkować błędami pracy falowników i przekroczeniem tolerancji napięciowych dla podzespołów automatyki.
Izolacje i powłoki – odporność na środowisko pracy
Przewody do urządzeń dźwignicowych nie mogą być standardowym produktem przemysłowym. Ich izolacja musi być odporna nie tylko na wysoką temperaturę pracy, ale również na promieniowanie UV, mgły olejowe, wodę, pył i agresywne czynniki chemiczne. Z tego względu bardzo ważny jest wybór odpowiedniego tworzywa izolacyjnego – zwykłe PVC w wielu przypadkach okaże się niewystarczające.
W praktyce dla aplikacji dźwignicowych stosuje się przewody z izolacją PUR (poliuretan) lub TPE (termoplastyczny elastomer), które zachowują elastyczność w niskich temperaturach, są odporne na ścieranie oraz nie wchłaniają wilgoci. Ich powierzchnia nie pęka przy zginaniu i nie sztywnieje w warunkach zimowych, co ma kluczowe znaczenie w przypadku suwnic pracujących na zewnątrz lub w nieogrzewanych halach.
Izolacja przewodu pełni nie tylko funkcję dielektryczną, ale również mechaniczną – chroni wnętrze kabla przed naprężeniami, mikrouderzeniami i odkształceniami, które powstają przy dynamicznej pracy urządzenia. Dlatego wybór taniego przewodu o niezweryfikowanej odporności może okazać się oszczędnością tylko pozorną.
Zabezpieczenia przed przepięciami i zwarciami – bezpieczeństwo systemu
W instalacjach zasilających urządzenia dźwignicowe bardzo ważną rolę odgrywają systemy zabezpieczające przed skutkami zwarć i przepięć. Choć nie są one bezpośrednio związane z samym przewodem, to właśnie jakość i konstrukcja kabla ma wpływ na ich skuteczność. Przewody powinny być odporne na działanie impulsów napięciowych, nie mogą przewodzić zakłóceń elektromagnetycznych do układów sterowania, a ich ekranowanie (jeśli występuje) musi być poprawnie uziemione i zakończone zgodnie z wymaganiami producenta.
Dobrą praktyką w projektowaniu instalacji dźwignicowych jest stosowanie przewodów o podwyższonej wytrzymałości napięciowej oraz odpowiednich zabezpieczeń w rozdzielnicy: wyłączników nadprądowych, różnicowoprądowych i przeciwprzepięciowych. W ten sposób nie tylko chronimy przewód, ale również wszystkie urządzenia do niego podłączone.
Przewody sterownicze – precyzja i niezawodność transmisji sygnału
W nowoczesnych systemach dźwignicowych przewody sterownicze pełnią równie ważną rolę jak zasilające, choć ich zadania są zupełnie inne. To właśnie one odpowiadają za precyzyjną komunikację między elementami automatyki, urządzeniami bezpieczeństwa, czujnikami położenia czy enkoderami. Zakłócenia w transmisji sygnału lub błędny dobór przewodów mogą skutkować nie tylko chwilową utratą kontroli nad urządzeniem, ale również niebezpiecznymi sytuacjami operacyjnymi.
W praktyce nie istnieje jeden uniwersalny przewód sterowniczy do wszystkich zastosowań. W zależności od środowiska, typu urządzenia, rodzaju transmisji danych i sposobu prowadzenia kabli, należy dobrać przewód spełniający konkretne parametry elektryczne, mechaniczne i EMC. Co ważne – przewody sterownicze zawsze powinny być traktowane jako komponent o wysokiej strategicznej wartości, a nie jako „dodatkowy kabel sygnałowy”.
Klasyczny przewód sterowniczy różni się od zasilającego już na etapie konstrukcji. Przede wszystkim posiada większą liczbę żył, często cieńszych, ale za to bardziej elastycznych, skręcanych w grupy robocze lub warstwowo. Dzięki temu przewód lepiej znosi ruchy skrętne i zginające, co jest istotne w aplikacjach dynamicznych – np. w firanach kablowych lub prowadnikach.
Warto również zwrócić uwagę na sposób ekranowania. W nowoczesnych urządzeniach dźwignicowych coraz częściej występuje współpraca przewodów sterowniczych z układami impulsowymi, falownikami czy systemami PLC. Obecność silnych pól elektromagnetycznych wymaga stosowania ekranów miedzianych, foli aluminiowych lub kombinowanych, które skutecznie chronią przed zakłóceniami EMI i RFI.
Nie bez znaczenia jest również kolorystyka żył, która musi być zgodna z normami PN-EN i ułatwiać szybką diagnostykę oraz bezpieczny montaż. W urządzeniach o dużej liczbie punktów sterowania warto rozważyć zastosowanie kabli z numeracją żył lub drukowanym oznaczeniem funkcyjnym.
Ekranowanie i odporność na zakłócenia – podstawa komunikacji bez błędów
W suwnicach wyposażonych w nowoczesne falowniki, czujniki bezdotykowe, enkodery czy systemy komunikacji szeregowej, stabilność sygnału ma kluczowe znaczenie dla pracy całego systemu. Zakłócenia elektromagnetyczne, jakie generują elementy napędowe, mogą powodować przekłamania danych, niestabilność pracy oraz błędne sygnały sterujące, jeśli przewody nie są odpowiednio zabezpieczone.
Z tego względu stosowanie ekranowanych przewodów sterowniczych jest nie tyle zaleceniem, co standardem. Ekran może mieć formę oplotu miedzianego, taśmy aluminiowej lub ich kombinacji. Kluczowe jest jednak jego właściwe zakończenie – ekranowanie musi być podłączone do uziemienia w sposób zgodny z zaleceniami producenta, bez tworzenia tzw. pętli masy.
Przy większych długościach przewodów i dużej ilości sygnałów o niskim napięciu należy również zadbać o separację kabli sterowniczych od zasilających, zarówno fizycznie (inne trasy), jak i elektrycznie (osobne obwody, separatory, filtry).
Kable hybrydowe i magistrale danych – kiedy standard już nie wystarcza
W nowoczesnych systemach sterowania coraz częściej stosuje się tzw. przewody hybrydowe – łączące w jednej konstrukcji żyły zasilające, sterownicze oraz przewody transmisji danych. To rozwiązanie oszczędza miejsce w trasach kablowych i skraca czas montażu, ale wymaga bardzo precyzyjnego doboru i wysokiej klasy materiałów izolacyjnych.
W suwnicach z komunikacją sieciową (np. CAN, ProfiBus, EtherCAT) niezbędne jest zastosowanie przewodów magistralnych – odpornych na skręt, z ekranowaniem pary skrętnej i odpowiednim dopasowaniem impedancji. Przewody te muszą spełniać normy IEC i być przeznaczone do pracy w ruchu, jeśli są prowadzone w systemach dynamicznych.
Ruchome aplikacje – przewody w firanach kablowych i prowadnikach
Ruch to jeden z najbardziej obciążających czynników w kontekście eksploatacji kabli. W suwnicach, żurawiach czy systemach transportu bliskiego przewody są poddawane ciągłym cyklom zginania, rozciągania, a często również skręcania. Ich trwałość zależy nie tylko od jakości materiałów, ale przede wszystkim od dostosowania konstrukcji przewodu do warunków dynamicznych. Ignorowanie tych wymagań to prosta droga do awarii – i to nie pojedynczego kabla, lecz całego systemu sterowania lub zasilania.
Najważniejszym parametrem, który decyduje o tym, czy przewód nadaje się do pracy w ruchu, jest minimalny promień gięcia. Producenci kabli precyzyjnie określają ten parametr, biorąc pod uwagę setki tysięcy, a często miliony cykli pracy. Jeżeli podczas projektowania systemu firany kablowej lub prowadnika nie zostanie zachowany ten promień – żywotność przewodu drastycznie spadnie.
Dlatego każdy przewód stosowany w systemach ruchomych musi być konstrukcyjnie przygotowany do pracy cyklicznej. Elastyczność osiąga się dzięki odpowiedniemu skręcaniu żył, zastosowaniu powłok TPE lub PUR oraz zmniejszeniu tarcia wewnętrznego między warstwami kabla. W systemach prowadników kablowych kluczowe jest też, aby przewód zachowywał stały promień gięcia i nie „pracował” na boki.
Choć wszystkie te systemy mają wspólny mianownik – przewód w ruchu – ich wymagania różnią się znacząco. W firanach kablowych kable są podtrzymywane przez wózki i poruszają się w jednym kierunku, w stosunkowo dużych łukach. Tutaj istotna jest odporność na uderzenia i ścieranie.
W prowadnikach kablowych, gdzie przewód „składa się” w harmonijkę, najważniejsza jest elastyczność i bardzo precyzyjna geometria kabla – musi on układać się idealnie w torze prowadnika bez efektu „pchania” lub „ciągnięcia”.