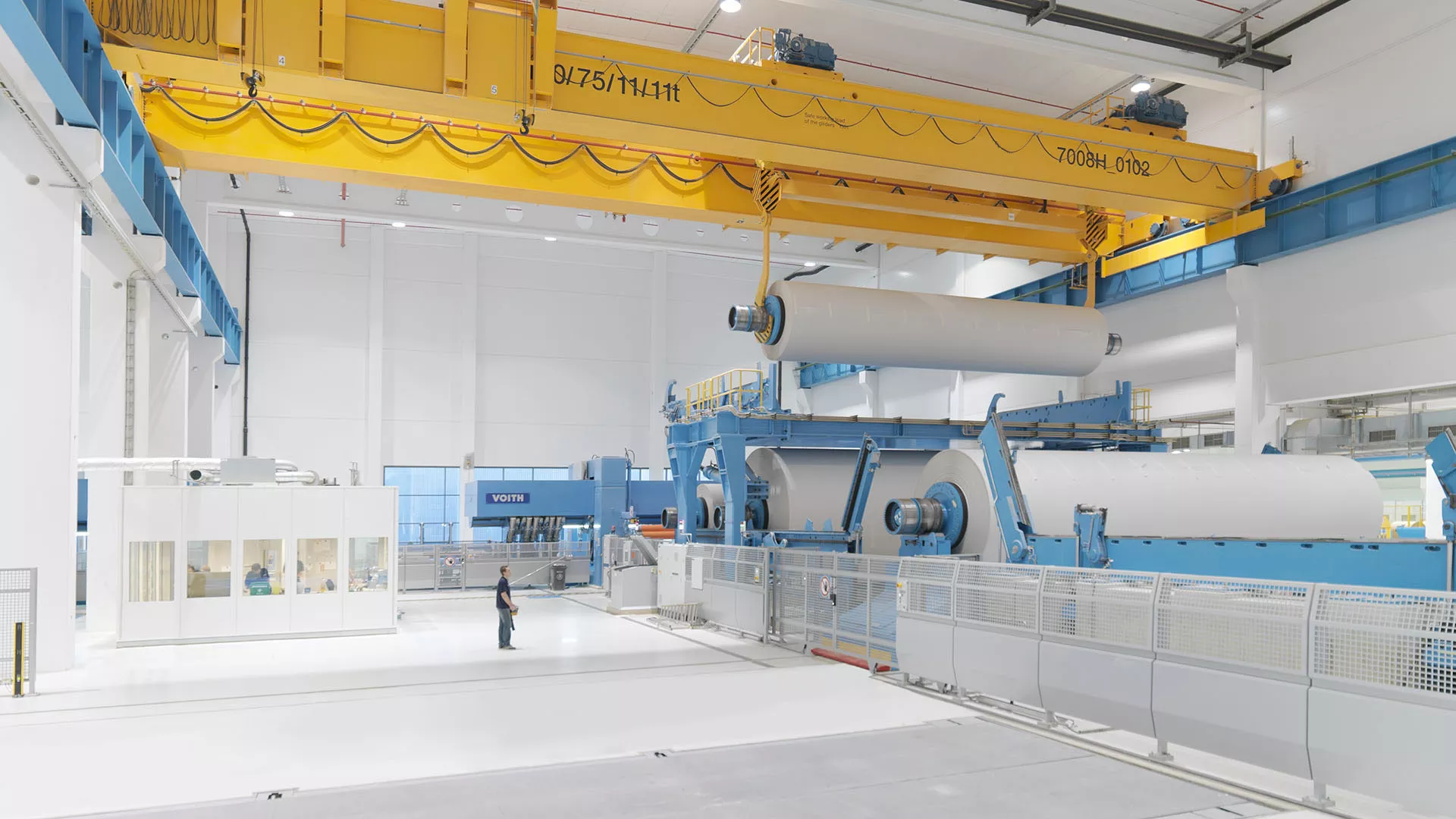
Osprzęt do suwnic – wszystko, co musisz wiedzieć
Osprzęt suwnicowy – jak wpływa na efektywność pracy?
W codziennej praktyce przemysłowej suwnica nie funkcjonuje jako samodzielny byt — jej realna wartość operacyjna ujawnia się dopiero w zestawie z odpowiednio dobranym osprzętem. Właśnie ten, często niedoceniany element konstrukcji, decyduje o tym, czy urządzenie będzie w pełni funkcjonalne, bezpieczne i dopasowane do charakterystyki danego procesu produkcyjnego czy logistycznego.
Mówiąc wprost: nawet najlepsza suwnica, wyposażona w nowoczesne mechanizmy jezdne i zaawansowany układ podnoszenia, bez właściwego osprzętu będzie urządzeniem o ograniczonej użyteczności. To właśnie osprzęt determinuje, jakiego rodzaju ładunki możemy podnosić, z jaką precyzją je manipulować oraz w jakim tempie prowadzić operacje przeładunkowe bez kompromisów w zakresie bezpieczeństwa.
Każdy z nas, kto zawodowo zarządza suwnicami lub odpowiada za Utrzymanie Ruchu w zakładzie przemysłowym, doskonale wie, że ogromne znaczenie ma powtarzalność, niezawodność i przewidywalność procesu. Odpowiednio skonfigurowany osprzęt to jeden z tych elementów, który w praktyce pozwala eliminować błędy operacyjne, skracać czas cyklu i zmniejszać ryzyko wystąpienia sytuacji awaryjnych.
Dobrze dobrany wciągnik, optymalnie poprowadzone zasilanie, niezawodne ograniczniki przeciążeniowe, ergonomiczna kaseta sterownicza — wszystkie te elementy stanowią integralną część większego systemu. Ich jakość oraz sposób integracji z konstrukcją suwnicy bezpośrednio przekładają się na komfort pracy operatora, a co za tym idzie – na wydajność całego procesu technologicznego. Co ważne, inwestycja w lepszy osprzęt to nie tylko kwestia wygody, ale również konkretne oszczędności w dłuższej perspektywie: mniej przestojów, niższe zużycie energii, mniejsze ryzyko kolizji czy uszkodzeń ładunku.
Czym różni się osprzęt standardowy od specjalistycznego?
Na rynku dostępnych jest wiele rozwiązań „katalogowych”, które pełnią funkcję tzw. osprzętu standardowego. Sprawdzają się one w wielu aplikacjach o powtarzalnym charakterze — typowe ładunki, umiarkowane warunki środowiskowe, niewielka zmienność parametrów pracy. Takie podejście może być uzasadnione w prostych instalacjach lub przy krótkoterminowych projektach.
Jednak w większości profesjonalnych zastosowań przemysłowych kluczowe staje się indywidualne dopasowanie osprzętu do potrzeb konkretnego zakładu. Mówimy wtedy o rozwiązaniach specjalistycznych — zaprojektowanych na wymiar, uwzględniających specyfikę ładunku, intensywność pracy, warunki otoczenia, a także wymogi prawne i branżowe (np. ATEX, HACCP, GOST-R).
Osprzęt specjalistyczny to nie tylko większa trwałość, ale przede wszystkim elastyczność operacyjna. Umożliwia on obsługę ładunków niestandardowych, pracę w warunkach szczególnych (np. wysokie zapylenie, niskie temperatury, strefy zagrożone wybuchem) oraz lepszą integrację z systemami automatyki czy logistyki wewnętrznej. Warto zaznaczyć, że dobrze zaprojektowany i wdrożony osprzęt specjalistyczny nie musi oznaczać znaczącego wzrostu kosztów inwestycyjnych — często kluczową rolę odgrywa tutaj doświadczenie producenta oraz jakość procesu doradczego.
Wciągniki i wciągarki – serce systemu podnoszenia
Układ podnoszenia to kluczowy komponent każdej suwnicy. Jego jakość i konfiguracja decydują nie tylko o udźwigu, ale także o płynności i precyzji operacji transportowych. W praktyce oznacza to, że to właśnie wciągnik lub wciągarka jest tym elementem, który w największym stopniu wpływa na efektywność pracy urządzenia. Wybór konkretnego rozwiązania nie powinien być przypadkowy – konieczna jest analiza rzeczywistych warunków pracy, rodzaju ładunków oraz oczekiwanej intensywności eksploatacji.
Na rynku dostępne są dwa podstawowe typy urządzeń podnoszących: wciągniki oraz wciągarki. Wciągniki, zarówno linowe, jak i łańcuchowe, znajdują zastosowanie w standardowych aplikacjach, gdzie istotna jest kompaktowość, prostota montażu oraz wysoka niezawodność. Ich zaletą jest szybki dostęp do części eksploatacyjnych i stosunkowo łatwa konserwacja. Sprawdzają się doskonale w mniejszych i średnich udźwigach, gdzie priorytetem jest ekonomiczność i elastyczność montażu w różnych konfiguracjach przestrzennych.
Z kolei wciągarki bębnowe to rozwiązania przeznaczone do zadań wymagających większych sił podnoszenia i pracy w cyklach ciągłych. Charakteryzują się one wyższą trwałością mechaniczną, możliwością pracy z większą długością liny oraz możliwością zastosowania zaawansowanych układów sterowania i zabezpieczeń. Ich zastosowanie jest szczególnie uzasadnione w przemyśle ciężkim, hutnictwie, stoczniach oraz przy obsłudze dużych gabarytowo elementów.
Kluczowe parametry techniczne, które należy wziąć pod uwagę przy doborze urządzenia podnoszącego, to: dopuszczalny udźwig, prędkość podnoszenia, długość robocza liny lub łańcucha, klasa pracy (np. FEM 2m, 3m), sposób mocowania oraz możliwość integracji z systemami automatyki. Coraz częściej standardem staje się wyposażenie wciągników w enkodery, czujniki przeciążeniowe, ograniczniki krańcowe oraz układy awaryjnego zatrzymania. Umożliwiają one precyzyjne pozycjonowanie ładunku, zwiększają bezpieczeństwo i umożliwiają integrację z nowoczesnymi systemami nadzoru pracy suwnic.
Zestawy kołowe i elementy jezdne – precyzyjne prowadzenie na torowisku
Układ jezdny suwnicy odpowiada za jej przemieszczanie wzdłuż torowiska i musi zapewniać maksymalną stabilność, płynność oraz odporność na zużycie. Zestawy kołowe to elementy o strategicznym znaczeniu – ich jakość wykonania i sposób montażu bezpośrednio przekładają się na żywotność całego urządzenia oraz poziom wibracji i hałasu generowanego podczas pracy. Wymagania wobec tych komponentów są szczególnie wysokie w środowiskach o intensywnym wykorzystaniu suwnic, gdzie każdy dzień przestoju oznacza realne straty operacyjne.
Podstawowy podział obejmuje koła napędowe oraz bierne. Koła napędowe przenoszą moment obrotowy z silnika na torowisko, odpowiadając za ruch urządzenia. Koła bierne pełnią funkcję toczną, zapewniając stabilność prowadzenia. W obu przypadkach materiał ma znaczenie kluczowe – najczęściej stosuje się stal gatunkową o wysokiej twardości, obrabianą cieplnie dla zwiększenia odporności na ścieranie. W aplikacjach specjalnych (np. z wysoką wilgotnością lub zapyleniem) możliwe jest zastosowanie materiałów o podwyższonej odporności korozyjnej lub powłok ochronnych.
Równie istotnym elementem zestawów kołowych są systemy łożyskowania. To one decydują o tym, jak suwnica zachowuje się przy zmianie kierunku jazdy, w czasie hamowania czy przy nierównym torowisku. Stosowane są rozwiązania kulkowe, baryłkowe oraz stożkowe – każdorazowo dopasowane do warunków eksploatacji. Dobrą praktyką jest również stosowanie uszczelnień labiryntowych i smarowania centralnego, co znacząco wydłuża okres międzyserwisowy.
Zestawy kołowe coraz częściej wyposażane są w systemy regulacji geometrii toru jazdy, co pozwala na precyzyjne ustawienie osi i eliminację naprężeń wynikających z niedoskonałości montażowych. Niewłaściwe ustawienie kół może prowadzić do nadmiernego zużycia szyn, zwiększonego oporu toczenia, a w konsekwencji – do uszkodzeń konstrukcji suwnicy. Dlatego tak ważne jest, by elementy jezdne pochodziły od sprawdzonych producentów i były każdorazowo dobierane z uwzględnieniem specyficznych wymagań aplikacji.
Systemy zasilania suwnic – przewody, festony, szynoprzewody
Zasilanie suwnicy to jeden z fundamentów jej niezawodnej pracy. Bez stabilnego i bezpiecznego doprowadzenia energii elektrycznej do wszystkich mechanizmów — zarówno napędowych, jak i sterujących — niemożliwe jest utrzymanie ciągłości produkcji oraz zachowanie parametrów technicznych wymaganych w danym procesie technologicznym. Systemy zasilania suwnic różnią się konstrukcyjnie, jednak ich podstawową funkcją jest dostarczanie mocy do urządzenia w sposób bezawaryjny, odporny na czynniki środowiskowe i możliwie mało inwazyjny dla infrastruktury.
W przemyśle stosowane są dwa główne typy zasilania suwnic: systemy kablowe (głównie festonowe) oraz nowocześniejsze rozwiązania oparte o szynoprzewody. Każde z nich ma swoje zalety i zastosowania, dlatego ich dobór powinien być zawsze poprzedzony analizą środowiska pracy, rozpiętości toru jazdy oraz parametrów eksploatacyjnych urządzenia.
Systemy festonowe, znane również jako kablowe prowadnice wózkowe, stosowane są najczęściej w suwnicach o mniejszych rozmiarach, w środowiskach o umiarkowanym poziomie zanieczyszczeń oraz tam, gdzie kluczowa jest prostota montażu i łatwość konserwacji. Przewody płaskie lub okrągłe są zawieszone na rolkach poruszających się wzdłuż prowadnicy, co pozwala na dynamiczne dopasowanie długości kabla w trakcie ruchu wózka lub całej suwnicy. Kluczowe znaczenie ma tutaj dobór przekroju przewodów, odporność izolacji na promienie UV, oleje, wilgoć oraz temperaturę pracy.
Alternatywą dla klasycznego systemu festonowego są szynoprzewody, które zapewniają stały kontakt elektryczny przez szczotki i wózki odbiorcze. Takie rozwiązania znajdują zastosowanie wszędzie tam, gdzie suwnice pracują intensywnie, a ich tor jazdy jest długi lub wielosegmentowy. Szynoprzewody eliminują problem zwisających kabli, są mniej narażone na uszkodzenia mechaniczne i lepiej sprawdzają się w środowiskach o dużym zapyleniu, wilgotności lub tam, gdzie wymagana jest ciągła praca bez przestojów technicznych.
Niezależnie od typu systemu zasilania, kluczowe jest jego odpowiednie zabezpieczenie – zarówno mechaniczne, jak i elektryczne. Stosowanie ograniczników przepięć, wyłączników bezpieczeństwa, uziemień oraz właściwego prowadzenia przewodów w strefach narażonych na uszkodzenia mechaniczne to podstawowe działania, które zapewniają wieloletnią bezawaryjną eksploatację suwnicy.
Sterowanie suwnicą – od kaset kablowych po pilotaż bezprzewodowy
System sterowania suwnicą jest nie mniej istotny niż jej mechaniczne komponenty. To właśnie za jego pośrednictwem operator komunikuje się z urządzeniem, wydaje polecenia ruchu, zatrzymania czy zmiany kierunku pracy. Od jakości i ergonomii tego systemu zależy komfort pracy, szybkość operacji oraz – co najważniejsze – bezpieczeństwo. Wybór odpowiedniego sposobu sterowania powinien być każdorazowo poprzedzony analizą warunków eksploatacji, typu wykonywanych zadań oraz kompetencji personelu obsługującego.
Podstawowym i nadal powszechnie stosowanym rozwiązaniem są kasety sterownicze kablowe, montowane na przewodzie spiralnym lub prowadzone w systemie festonowym. Ich zaletą jest bezpośrednie połączenie elektryczne z szafą sterującą suwnicy, co przekłada się na niezawodność transmisji sygnału. Dodatkowo są one wyjątkowo odporne na zakłócenia elektromagnetyczne oraz awarie systemowe. Dobrze zaprojektowana kaseta powinna posiadać odpowiedni stopień ochrony IP, czytelne przyciski, a także funkcje awaryjnego zatrzymania i sygnalizacji.
Coraz większą popularnością w nowoczesnych zakładach cieszy się jednak sterowanie radiowe, które oferuje operatorowi swobodę poruszania się i obserwacji przestrzeni pracy z bezpiecznej odległości. Piloty bezprzewodowe wykorzystują częstotliwości radiowe odporne na zakłócenia, a dodatkowo są wyposażone w systemy autoryzacji, redundancji sygnału i automatycznej detekcji błędów. Nowoczesne układy radiowe umożliwiają także zdalne diagnozowanie problemów oraz współpracę z wieloma suwnicami jednocześnie w ramach jednego systemu.
W suwnicach pracujących w trybie zautomatyzowanym lub półautomatycznym, coraz częściej stosuje się sterowanie za pomocą paneli HMI, systemów PLC oraz integrację z nadrzędnymi systemami informatycznymi – np. MES, WMS, ERP. Takie rozwiązania umożliwiają nie tylko bezpośrednie sterowanie ruchem, ale również zarządzanie kolejkami zleceń, nadzór nad cyklem pracy urządzenia oraz rejestrowanie wszystkich zdarzeń operacyjnych. To realna wartość dodana, zwłaszcza w zakładach produkcyjnych o dużym stopniu automatyzacji i wysokiej presji czasowej.