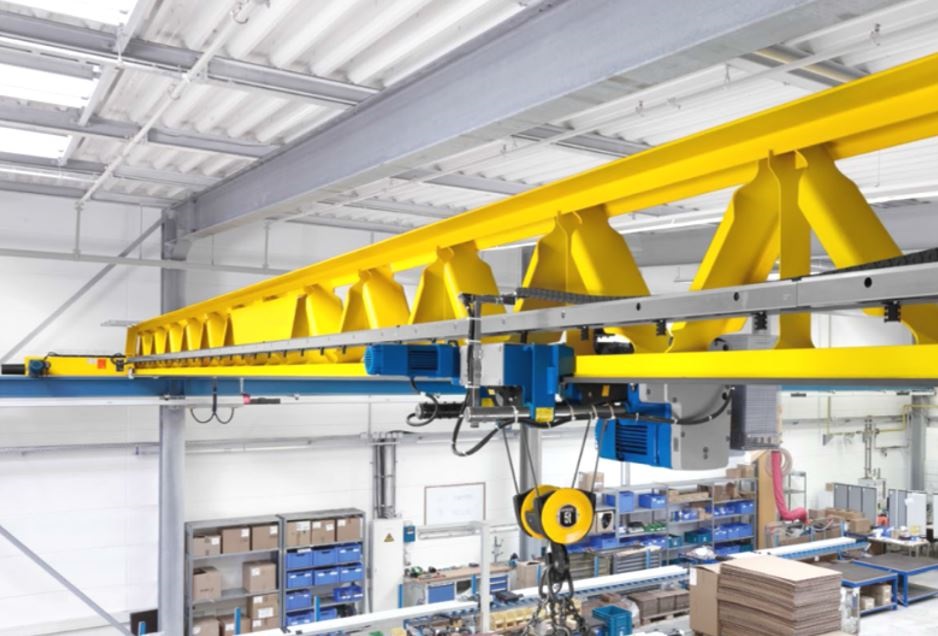
Firany kablowe w suwnicach – wszystko, co musisz wiedzieć
Gdzie stosujemy firany kablowe?
W systemach transportu bliskiego, zwłaszcza tam, gdzie mamy do czynienia z dynamicznym przemieszczaniem się elementów roboczych suwnicy, jednym z najskuteczniejszych rozwiązań z zakresu zasilania i przesyłu sygnałów są firany kablowe. Ich zastosowanie wynika bezpośrednio z potrzeby prowadzenia przewodów w sposób bezpieczny, elastyczny i nieingerujący w konstrukcję urządzenia czy strukturę hali. Dobrze zaprojektowany system firany kablowej gwarantuje ciągłość pracy nawet w środowiskach o wysokiej intensywności operacyjnej.
Suwnice pomostowe – dominujące zastosowanie firan kablowych
Najczęstszym miejscem wykorzystania firan kablowych są suwnice pomostowe, zarówno jedno-, jak i dwudźwigarowe. W suwnicach jednodźwigarowych firany kablowe montuje się zazwyczaj na dolnym pasie dźwigara, prowadząc kable zasilające wciągnik wzdłuż toru jego ruchu. Ich zadaniem jest zapewnienie płynnego przesuwu przewodów w trakcie pracy wózka oraz ochrona kabla przed przetarciem, nadmiernym zgięciem czy niekontrolowanym skrętem.
W wersjach dwudźwigarowych, gdzie wózek suwnicowy porusza się pomiędzy dźwigarami na górnym torze, system firan mocowany jest najczęściej na specjalnej konstrukcji pomocniczej. Pozwala to prowadzić kable nad wózkiem i zredukować ryzyko kolizji z elementami ładunku czy innym wyposażeniem hali. Dzięki swojej modułowej budowie, firany kablowe można dopasować niemal do każdej geometrii suwnicy i dostosować ich długość oraz promień pracy do parametrów konkretnego urządzenia.
Wciągniki i wciągarki z przesuwem – elastyczne prowadzenie przewodów
Drugim obszarem, gdzie firany kablowe znajdują zastosowanie w sposób systemowy, są wciągniki i wciągarki suwnicowe, które przemieszczają się po torze jezdnym, a wymagają jednoczesnego zasilania oraz przesyłu sygnałów sterujących. Firana umożliwia podłączenie wciągnika do źródła zasilania bez ryzyka plątania się przewodów oraz ich przypadkowego uszkodzenia. W tym przypadku długość i promień pracy systemu muszą być idealnie dopasowane do zakresu ruchu urządzenia oraz cyklu roboczego. W zakładach, gdzie praca prowadzona jest w systemie trzyzmianowym, niewłaściwe prowadzenie kabla może doprowadzić do jego uszkodzenia nawet w ciągu kilku dni – dlatego tak ważna jest jakość i precyzja montażu.
Różnorodne środowiska pracy – od przemysłu ciężkiego po magazyny
Firany kablowe znajdują zastosowanie w bardzo szerokim spektrum branż, co jest efektem ich dużej uniwersalności oraz relatywnie prostej adaptacji do różnych warunków pracy. W przemyśle ciężkim, takim jak hutnictwo, odlewnictwo czy produkcja konstrukcji stalowych, wykorzystuje się je do prowadzenia kabli odpornych na wysokie temperatury, oleje i pyły. Z kolei w zakładach zajmujących się produkcją żywności, leków lub komponentów elektronicznych stosuje się wersje o podwyższonej odporności chemicznej i zgodne z restrykcyjnymi normami higienicznymi.
W magazynach wysokiego składowania oraz centrach logistycznych firany kablowe często współpracują z suwnicami automatycznymi lub półautomatycznymi, gdzie istotna jest nie tylko trwałość mechaniczna, ale również bezawaryjna komunikacja między wózkiem suwnicowym a centralnym systemem sterowania. Systemy te muszą być odporne na wielokrotne cykle pracy, zmienne temperatury otoczenia oraz częste przejazdy na pełnym obciążeniu.
Budowa systemu firan kablowych – komponenty i ich funkcje
System firan kablowych, choć z pozoru może wydawać się prosty, jest w rzeczywistości precyzyjnie zaprojektowanym układem, którego każdy element ma jasno określoną funkcję techniczną i wpływa na trwałość oraz niezawodność całej instalacji. To właśnie właściwa konstrukcja firany kablowej decyduje o tym, czy zasilanie i sterowanie suwnicą będzie przebiegać bez zakłóceń nawet w trudnych warunkach przemysłowych.
Dobrze zaprojektowana firana kablowa umożliwia bezpieczne prowadzenie przewodów wzdłuż toru ruchu wózka suwnicowego lub wciągnika, zapobiegając ich skręcaniu, plątaniu, uszkodzeniu mechanicznemu czy przeciążeniu podczas pracy w cyklu roboczym. Każdy komponent, od kabla po wózek prowadzący, musi być dobrany z uwzględnieniem parametrów technicznych urządzenia dźwignicowego oraz charakterystyki środowiska pracy.
Kable płaskie i okrągłe – dostosowane do ruchu dynamicznego
Podstawą każdego systemu firany kablowej są odpowiednio dobrane przewody zasilające oraz sygnałowe. W zależności od wymagań aplikacyjnych stosuje się kable płaskie lub okrągłe, przy czym to wersje płaskie dominują w układach prowadzenia dynamicznego ze względu na lepszą odporność na wielokrotne zginanie w jednym kierunku.
Kable te projektowane są specjalnie z myślą o aplikacjach ruchomych – charakteryzują się dużą elastycznością, odpornością na mikrołamanie i działanie czynników zewnętrznych, takich jak oleje, UV czy ekstremalne temperatury. Ich izolacje są najczęściej wykonane z tworzyw takich jak PUR lub TPE, które zapewniają odpowiednią wytrzymałość mechaniczną i jednocześnie nie sztywnieją w niskich temperaturach. To niezwykle istotne w halach nieogrzewanych, gdzie suwnice pracują w pełnym zakresie sezonowym.
Dobrze dobrany przewód musi mieć także odpowiedni przekrój, dostosowany do mocy znamionowej odbiorników oraz długości linii, aby zminimalizować spadki napięć i zapewnić stabilność pracy urządzenia. W przypadku suwnic wyposażonych w nowoczesne sterowanie PLC, niezbędne jest również prowadzenie kabli sygnałowych lub magistral komunikacyjnych, które muszą być ekranowane i odporne na zakłócenia elektromagnetyczne.
Wózki jezdne – fundament bezpiecznego prowadzenia kabla
Wózki jezdne to elementy nośne firany kablowej, których zadaniem jest podtrzymywanie kabla na całej długości jego prowadzenia i umożliwienie jego ruchu synchronicznie z ruchem suwnicy lub wciągnika. Ich konstrukcja musi być zarówno lekka, jak i wytrzymała. Zazwyczaj wykonywane są z ocynkowanej stali lub tworzyw technicznych o wysokiej odporności na ścieranie. Kluczowe znaczenie ma precyzja prowadzenia – wózki powinny poruszać się płynnie po szynie lub lince nośnej, bez efektu zacinania, szarpania czy nadmiernych luzów.
Każdy wózek wyposażony jest w rolki łożyskowane, które minimalizują opory toczenia i przeciwdziałają nadmiernemu zużyciu komponentów. Przy projektowaniu trasy firany bardzo istotne jest właściwe rozstawienie wózków – zbyt duże odległości między nimi mogą powodować nadmierne zwisanie przewodów i prowadzić do ich deformacji, zwłaszcza w niskich temperaturach. Z kolei zbyt mały rozstaw generuje niepotrzebny opór i przyspiesza zużycie wózków.
Szyna jezdna lub lina nośna – stabilność trasy kablowej
Trasa ruchu firany kablowej musi być jednoznacznie zdefiniowana i trwała w czasie. W zależności od rodzaju systemu stosuje się szyny jezdne – najczęściej stalowe profile w kształcie litery „C” – lub liny stalowe naciągnięte na uchwyty końcowe. Oba rozwiązania mają swoje zalety: szyny zapewniają lepszą stabilność i są odporne na przypadkowe uderzenia, natomiast liny są łatwiejsze do montażu w trudno dostępnych miejscach i lżejsze konstrukcyjnie.
Elementy te muszą być odpowiednio zamocowane do konstrukcji suwnicy lub hali, a ich montaż powinien uwzględniać kompensację rozszerzalności termicznej i eliminację naprężeń wstępnych. W przypadku długich tras – powyżej kilkunastu metrów – zaleca się stosowanie prowadnic z segmentów dylatacyjnych lub uchwytów pływających, które pozwalają na swobodne wydłużanie i kurczenie się trasy bez generowania naprężeń na kablach.
Napinacze i odboje – kontrola długości i zakresu pracy
Każdy system firany kablowej musi mieć fizycznie zdefiniowany początek i koniec trasy ruchu. W tym celu stosuje się napinacze oraz odboje krańcowe. Napinacze, najczęściej sprężynowe lub śrubowe, zapewniają stałe napięcie w lince nośnej lub szynie prowadzącej, eliminując ryzyko „obwieszenia się” kabla i kontaktu z konstrukcją suwnicy lub ładunkiem. Z kolei odboje chronią wózki kablowe przed uderzeniem o konstrukcję nośną przy nagłym zatrzymaniu ruchu.
W zależności od prędkości i długości trasy zaleca się stosowanie różnego typu ograniczników – od mechanicznych po amortyzatory z elastomeru, które absorbują energię kinetyczną i chronią komponenty przed uszkodzeniem. Prawidłowo dobrane i zamontowane elementy końcowe mają kluczowe znaczenie dla trwałości systemu oraz komfortu pracy operatora.
Uchwyty i separatory – porządek w trasie kablowej
Aby firana kablowa spełniała swoje zadanie w sposób powtarzalny i bezawaryjny, niezbędne są odpowiednio rozmieszczone uchwyty oraz separatory, które stabilizują pozycję kabli i zapobiegają ich skręcaniu. W systemach wielokablowych lub takich, które prowadzą zarówno kable zasilające, jak i sygnałowe, separatory są wręcz niezbędne – umożliwiają równoległe ułożenie przewodów bez ich wzajemnego ściskania czy zakłócania transmisji danych.
Uchwyty montażowe, najczęściej wykonane z tworzyw odpornych na UV i oleje przemysłowe, muszą być solidnie zamocowane do ramy suwnicy lub struktury wsporczej. Ich dobór zależy od średnicy przewodów, liczby kabli prowadzonych równolegle oraz sił działających w trakcie cyklu roboczego.
Parametry techniczne – co decyduje o niezawodności firany kablowej?
Każdy, kto odpowiada za dobór lub serwisowanie firan kablowych w suwnicach, wie, że ich skuteczność nie zależy wyłącznie od rodzaju kabli czy jakości wózków prowadzących. Prawdziwa niezawodność całego systemu to wypadkowa wielu czynników technicznych, które – jeśli zostaną zignorowane – mogą prowadzić do przeciążeń, usterek, a w skrajnych przypadkach nawet do uszkodzenia suwnicy lub jej niespodziewanego przestoju. Poniżej omawiamy kluczowe parametry, które powinny zostać przeanalizowane jeszcze przed montażem systemu firany kablowej.
Promień gięcia – najczęściej ignorowany czynnik, który decyduje o trwałości
Jednym z podstawowych błędów projektowych jest nieuwzględnienie minimalnego promienia gięcia kabli w ruchu. Każdy przewód – niezależnie od tego, czy mówimy o kablu płaskim, okrągłym, ekranowanym czy zasilającym – posiada określony przez producenta promień gięcia dynamicznego, którego przekroczenie powoduje mikrołamanie struktury wewnętrznej izolacji i żył przewodzących. Efekt? Przyspieszone zużycie, uszkodzenia izolacji, spadki napięć, a w konsekwencji awarie i kosztowne przerwy w pracy.
Dlatego tak ważne jest, aby na etapie projektowania uwzględniać dokładne dane techniczne kabli, w tym właśnie promień gięcia oraz częstotliwość cykli roboczych. Im mniejszy promień – tym większe obciążenie dla struktury przewodu, zwłaszcza przy pracy wielozmianowej.
Długość toru jazdy i masa przewodów – wpływ na dynamikę systemu
Im dłuższy tor jazdy suwnicy lub wózka, tym większe wymagania stawiane są całemu systemowi prowadzenia kabli. W praktyce oznacza to konieczność doboru większej liczby wózków, optymalizacji rozstawu, a często również wzmocnienia struktury prowadzącej (np. poprzez zastosowanie szyny jezdnej zamiast liny). Dodatkowo dochodzi masa samych przewodów – często lekceważona na etapie projektowania, a mająca realny wpływ na momenty bezwładności, zużycie łożysk i żywotność napinaczy.
W systemach o dużej długości trasy (powyżej 25–30 metrów) stosowanie zbyt lekkich komponentów może skutkować efektem „kołysania się” firany przy hamowaniu lub nagłym ruszaniu. To nie tylko zagrożenie dla kabli, ale też dla operatora i stabilności procesu. Dlatego przy torach o znacznej długości szczególnie istotne jest sztywne prowadzenie trasy oraz precyzyjne zaprojektowanie punktów skrajnych.
Odporność kabli na warunki środowiskowe – nie każdy przewód sprawdzi się w hali
Z pozoru „zwykłe” kable do suwnic muszą sprostać wymaganiom znacznie przekraczającym standardy przewodów stacjonarnych. W zakładach przemysłowych przewody narażone są na: wahania temperatury, wilgoć, zapylenie, działanie mgieł olejowych, promieniowanie UV (w przypadku suwnic zewnętrznych) oraz intensywne drgania mechaniczne. Dlatego dobór kabli do firan musi uwzględniać klasę odporności na te czynniki.
Kable do zastosowań ruchomych powinny być wykonane z materiałów takich jak PUR, TPE lub specjalnie modyfikowany PVC – odporne na mikropęknięcia, uszkodzenia mechaniczne oraz działanie chemikaliów. W halach nieogrzewanych należy dodatkowo brać pod uwagę twardnienie izolacji w niskiej temperaturze oraz zdolność kabla do zachowania elastyczności nawet przy temperaturach rzędu -20°C.